EMG Prosthetic Arm
2023
Overview
This project integrated my passion for Arduino and 3D printing, into a functional prototype of a prosthetic arm. My aim for this project was to minimize the dramatic costs of conventional prosthetic limbs while replicating similar functionality and durability. It utilizes a series of 6 high torque servo motors, an Arduino board, an EMG sensor, and various other small electronics. By utilizing a pre-existing hand CAD model, I was able to integrate a forearm and mounting box to store the electronics.
The Arduino utilized MyoWare's EMG sensors to detect muscle contractions, detecting the duration of each contraction. This allowed the user to utilize various preset gestures and finger positions. In addition, a manual mode was integrated, allowing users to lengthen and contract the fingers as well as rotate the wrist.
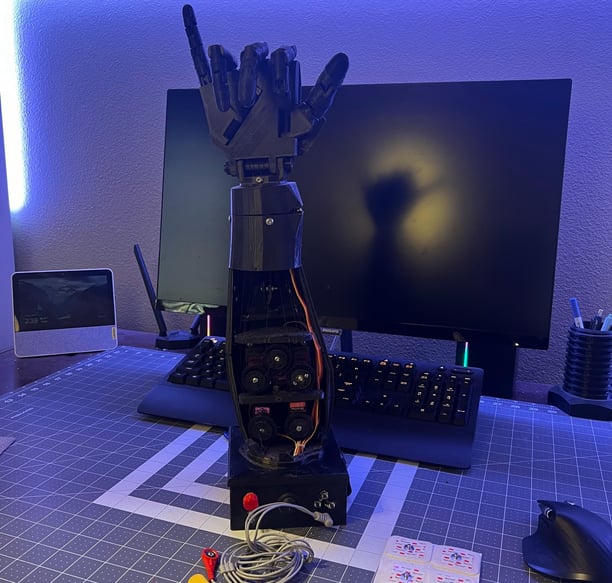
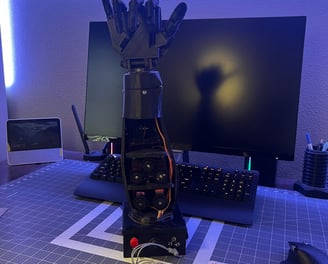
Process
The assembly and construction of the prosthetic limb were rather straightforward and direct, although some adjustments were made in the tolerances between finger joints and wrist flexion and rotation. Before integrating the EMG technology, I wired up a simple control unit to test functionality as an overall assembly before getting to the more challenging parts of the build.
Sourcing an inexpensive sensor was crucial to the objective of this project while still remaining reliable and easy to interface with. MYOWARE's muscle sensor module was a good compromise but could be a point of concern for future developments. In ideal conditions, the EMG sensor would display accurate data, but fluctuations in temperature or sweat would greatly reduce accuracy.
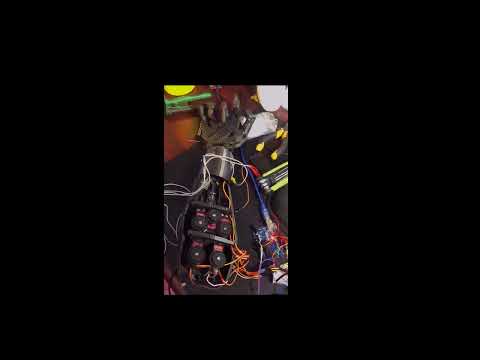
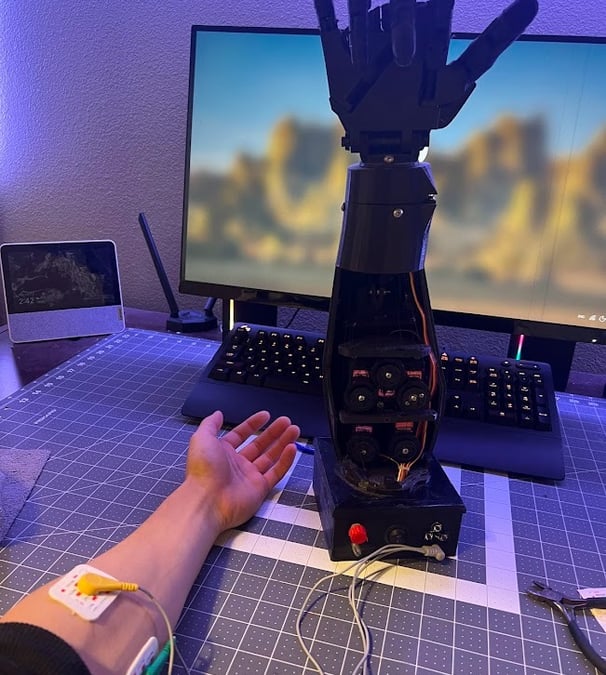
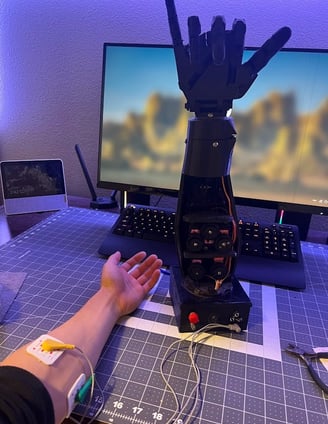
Result
Overall, this project was a great introduction to the possibilities of rapid prototyping and EMG innovation and is a project I would like to revisit in the future.